EZS Series
To drive the rotating threaded spindle – at the highest volume performance by means of a new winding technique. The motor shaft is constructed as a blind hole hollow shaft. The threaded spindle and the motor shaft are connected by a clamping assembly.
- 产品简介
- 产品特点
- 产品规格
- 产品尺寸
- 资料下载
To drive the rotating threaded spindle – at the highest volume performance by means of a new winding technique. The motor shaft is constructed as a blind hole hollow shaft. The threaded spindle and the motor shaft are connected by a clamping assembly.
Bearing design
Axial angular ball bearing acting on two sides for direct absorption of the threaded spindle forces.
Bearing design
Motor Brake
Optionally the motor b-side can be equipped with a permanent magnet holding brake.
EZ Brake
Power and Encoder Interface
- Rotating plug connectors with quick lock.
- Option: Supplied with mating connectors.
EZ Connection Method
Encoder
- Optical or inductive measuring principle
- High system accuracy with up to 23 bits resolution
- Up to 4096 recordable resolutions in multiturn version
- Electronic nameplate ensures fast and easy commissioning
- Compatible with STOBER drive controllers and drive controllers of many third-party manufacturers
Resolver
- High temperature resistance
- High vibration strength and shock resistance
Power and Encoder Interface One Cable Solution (OCS)
- Rotating plug connector with quick lock (connection lines between the encoder and drive controller are routed along in the motor's power cable).
- Option: Supplied with mating connector.
EZ Connection Method (OCS)
Encoder One Cable Solution (OCS)
HIPERFACE DSL One Cable Solution (OCS)
- Significantly reduced wiring effort by eliminating the encoder cable
- Significantly reduced space requirements by eliminating the encoder plug connector
- High system accuracy with up to 20 bits resolution
- Up to 4096 recordable resolutions in multiturn version
- Electronic nameplate ensures fast and easy commissioning
- Additional information transferred with the position value
Winding Protection
PTC thermistors are installed in STOBER synchronous servo motors as a configuration feature to implement thermal winding protection. This makes it possible for the motor to exceed the maximum permitted winding temperature with the appropriate devices turned off.
Paint Finish
- Housing and connector black RAL 9005
- Motor cover b-side magenta RAL 4010
Drive Controller Recommendation
- POSIDRIVE MDS 5000 with power range 0.75 to 45 kW
- POSIDYN SDS 5000 with power range 0.75 to 45 kW
- SD6 with power range 0.75 kW to 45 kW
- SI6 with power range 0.75 kW to 25.9 kW
For further information see Drive Controllers
Axial angular ball bearing acting on two sides for direct absorption of the threaded spindle forces.
Bearing design
Motor Brake
Optionally the motor b-side can be equipped with a permanent magnet holding brake.
EZ Brake
Power and Encoder Interface
- Rotating plug connectors with quick lock.
- Option: Supplied with mating connectors.
EZ Connection Method
Encoder
- Optical or inductive measuring principle
- High system accuracy with up to 23 bits resolution
- Up to 4096 recordable resolutions in multiturn version
- Electronic nameplate ensures fast and easy commissioning
- Compatible with STOBER drive controllers and drive controllers of many third-party manufacturers
Resolver
- High temperature resistance
- High vibration strength and shock resistance
Power and Encoder Interface One Cable Solution (OCS)
- Rotating plug connector with quick lock (connection lines between the encoder and drive controller are routed along in the motor's power cable).
- Option: Supplied with mating connector.
EZ Connection Method (OCS)
Encoder One Cable Solution (OCS)
HIPERFACE DSL One Cable Solution (OCS)
- Significantly reduced wiring effort by eliminating the encoder cable
- Significantly reduced space requirements by eliminating the encoder plug connector
- High system accuracy with up to 20 bits resolution
- Up to 4096 recordable resolutions in multiturn version
- Electronic nameplate ensures fast and easy commissioning
- Additional information transferred with the position value
Winding Protection
PTC thermistors are installed in STOBER synchronous servo motors as a configuration feature to implement thermal winding protection. This makes it possible for the motor to exceed the maximum permitted winding temperature with the appropriate devices turned off.
Paint Finish
- Housing and connector black RAL 9005
- Motor cover b-side magenta RAL 4010
Drive Controller Recommendation
- POSIDRIVE MDS 5000 with power range 0.75 to 45 kW
- POSIDYN SDS 5000 with power range 0.75 to 45 kW
- SD6 with power range 0.75 kW to 45 kW
- SI6 with power range 0.75 kW to 25.9 kW
For further information see Drive Controllers
Type | Nominal speed [1/min] | Nominal torque [Nm] | Nominal current [A] | Stall torque [Nm] | Nominal power [kW] | Maximum torque [Nm] | Mass moment of inertia dynamic [kgcm²] |
---|---|---|---|---|---|---|---|
EZS501 | 3000 | 3,85 – 5,1 | 3,65 – 4,7 | 4,3 – 5,45 | 1,2 – 1,6 | 16 | 6,5 |
EZS502 | 3000 | 6,9 – 10 | 5,3 – 7,8 | 7,55 – 10,9 | 2,2 – 3,1 | 31 | 8,8 |
EZS503 | 3000 | 9,1 – 14,1 | 6,7 – 10,9 | 10,7 – 15,6 | 2,9 – 4,4 | 43 | 11,1 |
EZS701 | 3000 | 6,65 – 9,35 | 6,8 – 9,5 | 7,65 – 10,2 | 2,1 – 2,9 | 20 | 20,3 |
EZS702 | 3000 | 11 – 16,3 | 7,75 – 11,8 | 13,5 – 19 | 3,5 – 5,1 | 41 | 25,6 |
EZS703 | 3000 | 15,3 – 23,7 | 10,8 – 18,2 | 19,7 – 27,7 | 4,8 – 7,4 | 65 | 30,8 |
EZS Series
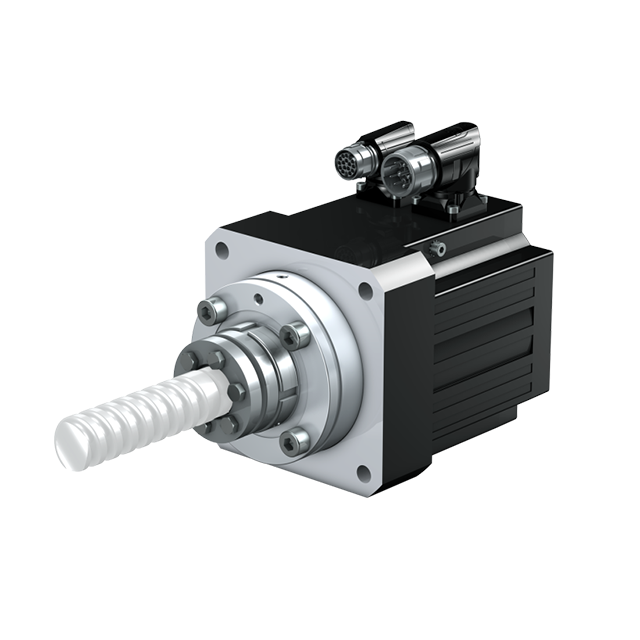
- 产品简介
- 产品特点
- 产品规格
- 产品尺寸
- 资料下载
To drive the rotating threaded spindle – at the highest volume performance by means of a new winding technique. The motor shaft is constructed as a blind hole hollow shaft. The threaded spindle and the motor shaft are connected by a clamping assembly.
Bearing design
Axial angular ball bearing acting on two sides for direct absorption of the threaded spindle forces.
Bearing design
Motor Brake
Optionally the motor b-side can be equipped with a permanent magnet holding brake.
EZ Brake
Power and Encoder Interface
- Rotating plug connectors with quick lock.
- Option: Supplied with mating connectors.
EZ Connection Method
Encoder
- Optical or inductive measuring principle
- High system accuracy with up to 23 bits resolution
- Up to 4096 recordable resolutions in multiturn version
- Electronic nameplate ensures fast and easy commissioning
- Compatible with STOBER drive controllers and drive controllers of many third-party manufacturers
Resolver
- High temperature resistance
- High vibration strength and shock resistance
Power and Encoder Interface One Cable Solution (OCS)
- Rotating plug connector with quick lock (connection lines between the encoder and drive controller are routed along in the motor's power cable).
- Option: Supplied with mating connector.
EZ Connection Method (OCS)
Encoder One Cable Solution (OCS)
HIPERFACE DSL One Cable Solution (OCS)
- Significantly reduced wiring effort by eliminating the encoder cable
- Significantly reduced space requirements by eliminating the encoder plug connector
- High system accuracy with up to 20 bits resolution
- Up to 4096 recordable resolutions in multiturn version
- Electronic nameplate ensures fast and easy commissioning
- Additional information transferred with the position value
Winding Protection
PTC thermistors are installed in STOBER synchronous servo motors as a configuration feature to implement thermal winding protection. This makes it possible for the motor to exceed the maximum permitted winding temperature with the appropriate devices turned off.
Paint Finish
- Housing and connector black RAL 9005
- Motor cover b-side magenta RAL 4010
Drive Controller Recommendation
- POSIDRIVE MDS 5000 with power range 0.75 to 45 kW
- POSIDYN SDS 5000 with power range 0.75 to 45 kW
- SD6 with power range 0.75 kW to 45 kW
- SI6 with power range 0.75 kW to 25.9 kW
For further information see Drive Controllers
Axial angular ball bearing acting on two sides for direct absorption of the threaded spindle forces.
Bearing design
Motor Brake
Optionally the motor b-side can be equipped with a permanent magnet holding brake.
EZ Brake
Power and Encoder Interface
- Rotating plug connectors with quick lock.
- Option: Supplied with mating connectors.
EZ Connection Method
Encoder
- Optical or inductive measuring principle
- High system accuracy with up to 23 bits resolution
- Up to 4096 recordable resolutions in multiturn version
- Electronic nameplate ensures fast and easy commissioning
- Compatible with STOBER drive controllers and drive controllers of many third-party manufacturers
Resolver
- High temperature resistance
- High vibration strength and shock resistance
Power and Encoder Interface One Cable Solution (OCS)
- Rotating plug connector with quick lock (connection lines between the encoder and drive controller are routed along in the motor's power cable).
- Option: Supplied with mating connector.
EZ Connection Method (OCS)
Encoder One Cable Solution (OCS)
HIPERFACE DSL One Cable Solution (OCS)
- Significantly reduced wiring effort by eliminating the encoder cable
- Significantly reduced space requirements by eliminating the encoder plug connector
- High system accuracy with up to 20 bits resolution
- Up to 4096 recordable resolutions in multiturn version
- Electronic nameplate ensures fast and easy commissioning
- Additional information transferred with the position value
Winding Protection
PTC thermistors are installed in STOBER synchronous servo motors as a configuration feature to implement thermal winding protection. This makes it possible for the motor to exceed the maximum permitted winding temperature with the appropriate devices turned off.
Paint Finish
- Housing and connector black RAL 9005
- Motor cover b-side magenta RAL 4010
Drive Controller Recommendation
- POSIDRIVE MDS 5000 with power range 0.75 to 45 kW
- POSIDYN SDS 5000 with power range 0.75 to 45 kW
- SD6 with power range 0.75 kW to 45 kW
- SI6 with power range 0.75 kW to 25.9 kW
For further information see Drive Controllers
Type | Nominal speed [1/min] | Nominal torque [Nm] | Nominal current [A] | Stall torque [Nm] | Nominal power [kW] | Maximum torque [Nm] | Mass moment of inertia dynamic [kgcm²] |
---|---|---|---|---|---|---|---|
EZS501 | 3000 | 3,85 – 5,1 | 3,65 – 4,7 | 4,3 – 5,45 | 1,2 – 1,6 | 16 | 6,5 |
EZS502 | 3000 | 6,9 – 10 | 5,3 – 7,8 | 7,55 – 10,9 | 2,2 – 3,1 | 31 | 8,8 |
EZS503 | 3000 | 9,1 – 14,1 | 6,7 – 10,9 | 10,7 – 15,6 | 2,9 – 4,4 | 43 | 11,1 |
EZS701 | 3000 | 6,65 – 9,35 | 6,8 – 9,5 | 7,65 – 10,2 | 2,1 – 2,9 | 20 | 20,3 |
EZS702 | 3000 | 11 – 16,3 | 7,75 – 11,8 | 13,5 – 19 | 3,5 – 5,1 | 41 | 25,6 |
EZS703 | 3000 | 15,3 – 23,7 | 10,8 – 18,2 | 19,7 – 27,7 | 4,8 – 7,4 | 65 | 30,8 |